Mathematical Foundations of Robotic Arms: An In-Depth Analysis
1. Rigid Body Transformations
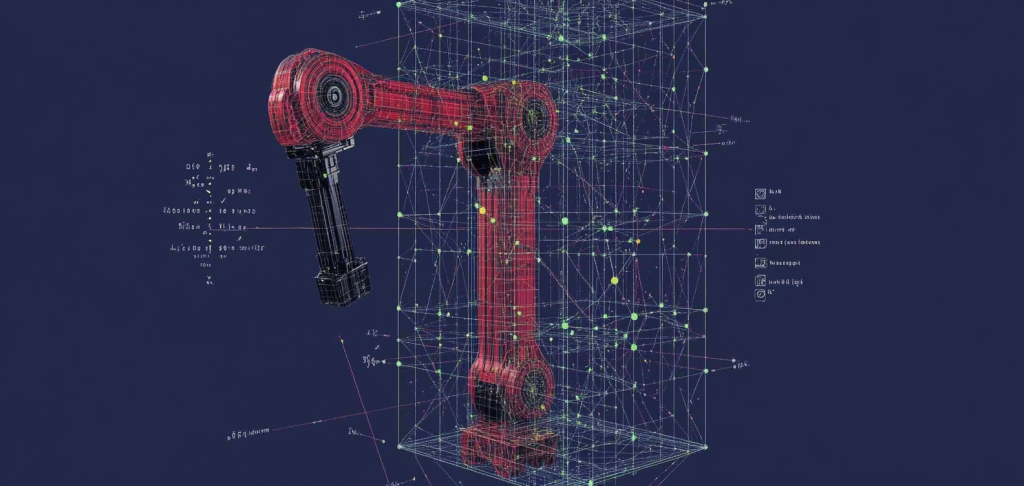
1.1 Rotation Matrices
A rotation matrix R ∈ SO(3) (Special Orthogonal Group) represents orientation in 3D space. For rotations around principal axes:
Around X-axis (Roll, φ):
Rx(φ) = [1 0 0 ]
[0 cos(φ) -sin(φ)]
[0 sin(φ) cos(φ)]
Around Y-axis (Pitch, θ):
Ry(θ) = [ cos(θ) 0 sin(θ)]
[ 0 1 0 ]
[-sin(θ) 0 cos(θ)]
Around Z-axis (Yaw, ψ):
Rz(ψ) = [cos(ψ) -sin(ψ) 0]
[sin(ψ) cos(ψ) 0]
[0 0 1]
1.2 Homogeneous Transformations
A homogeneous transformation matrix T ∈ SE(3) (Special Euclidean Group) combines rotation and translation:
T = [R p]
[0 1]
where:
- R is the 3×3 rotation matrix
- p is the 3×1 translation vector
- 0 is a 1×3 zero vector
2. Advanced Kinematics
2.1 Denavit-Hartenberg Parameters Extended
For a link i, the complete transformation matrix using DH parameters:
A_i = Rot(z,θi)Trans(z,di)Trans(x,ai)Rot(x,αi)
Expanded form:
A_i = [cos(θi) -sin(θi)cos(αi) sin(θi)sin(αi) ai*cos(θi)]
[sin(θi) cos(θi)cos(αi) -cos(θi)sin(αi) ai*sin(θi)]
[0 sin(αi) cos(αi) di ] [0 0 0 1 ]
2.2 Velocity Kinematics
The geometric Jacobian J relates joint velocities to end-effector velocities:
[v] = J(θ)[θ̇]
[ω]
For an n-DOF manipulator:
J = [Jv] ∈ R^(6×n)
[Jω]
For revolute joints, the ith column of J is:
Ji = [zi-1 × (pn - pi-1)]
[zi-1 ]
where:
- zi-1 is the axis of rotation of joint i
- pn is the position of the end-effector
- pi-1 is the position of joint i
3. Dynamic Modeling
3.1 Lagrangian Formulation
The Lagrangian L = K – P, where:
- K is kinetic energy
- P is potential energy
For an n-DOF manipulator:
K = (1/2)θ̇ᵀM(θ)θ̇
where M(θ) is the mass matrix:
M(θ) = ∑(i=1 to n) [Jviᵀmi Jvi + Jωiᵀ Ii Jωi]
3.2 Equations of Motion
The complete dynamic model:
M(θ)θ̈ + C(θ,θ̇)θ̇ + G(θ) = τ - JᵀF
where:
- C(θ,θ̇)θ̇ represents Coriolis and centrifugal forces
- G(θ) is the gravity vector
- τ is the joint torque vector
- F represents external forces
- J is the Jacobian matrix
The Christoffel symbols for computing C(θ,θ̇):
cijk = (1/2)[∂mij/∂θk + ∂mik/∂θj - ∂mjk/∂θi]
4. Advanced Control Theory
4.1 Computed Torque Control
The computed torque control law:
τ = M(θ)[θ̈d + Kv(θ̇d - θ̇) + Kp(θd - θ)] + C(θ,θ̇)θ̇ + G(θ)
where:
- θd, θ̇d, θ̈d are desired trajectories
- Kp, Kv are positive definite gain matrices
4.2 Impedance Control
The impedance control relationship:
M(ẍ - ẍd) + B(ẋ - ẋd) + K(x - xd) = F
where:
- M, B, K are desired inertia, damping, and stiffness matrices
- x, ẋ, ẍ are position, velocity, and acceleration
- F is the external force
5. Trajectory Planning
5.1 Cubic Polynomial Trajectory
For a trajectory from θ0 to θf in time tf:
θ(t) = a0 + a1t + a2t² + a3t³
where coefficients are found by solving:
[1 0 0 0 ][a0] = [θ0]
[1 tf tf² tf³][a1] = [θf]
[0 1 0 0 ][a2] = [θ̇0]
[0 1 2tf 3tf²][a3] = [θ̇f]
5.2 Quintic Polynomial Trajectory
For smoother motion with controlled acceleration:
θ(t) = a0 + a1t + a2t² + a3t³ + a4t⁴ + a5t⁵
6. Workspace Analysis
6.1 Manipulability Measure
Yoshikawa’s manipulability measure:
w = √(det(J(θ)J(θ)ᵀ))
6.2 Condition Number
For assessing dexterity:
κ(J) = σmax(J)/σmin(J)
where σmax and σmin are the maximum and minimum singular values of J.
Conclusion
These mathematical foundations form the basis for understanding and controlling robotic manipulators. The interplay between kinematics, dynamics, and control theory enables the precise manipulation required in modern robotics applications. Advanced topics like optimal control, adaptive control, and learning-based approaches build upon these fundamentals to create more sophisticated robotic systems.
2024 Hobbyist Robot Arm Comparison Guide: Finding Your Perfect Match
Quick Reference Table
Feature | RoboMaker RT6 | TinkerArm Pro | MakerBot X7 | CraftBot Arm | EduBot Basic |
---|---|---|---|---|---|
Price | $1,499 | $899 | $2,199 | $1,299 | $599 |
Degrees of Freedom | 6 | 4 | 7 | 6 | 4 |
Max Payload | 800g | 400g | 1.2kg | 600g | 250g |
Reach | 650mm | 450mm | 850mm | 600mm | 400mm |
Repeatability | ±0.1mm | ±0.2mm | ±0.05mm | ±0.15mm | ±0.3mm |
Base Rotation | 360° | 270° | 360° | 340° | 180° |
Communication | USB/WiFi/BT | USB | USB/ETH/WiFi | USB/WiFi | USB |
Software Support | ROS/Python | Arduino/Python | ROS/Python/C++ | Python | Blockly/Python |
Power Requirements | 24V, 3A | 12V, 2A | 24V, 4A | 24V, 2.5A | 12V, 1.5A |
Construction Material | Aluminum/Steel | ABS/Aluminum | All Aluminum | Aluminum/Plastic | ABS Plastic |
Detailed Analysis
RoboMaker RT6 ($1,499)
Best for: Advanced Hobbyists
Technical Specifications:
- Joint Speed: 90°/s (base) to 120°/s (wrist)
- Motor Type: NEMA 17 steppers with 256 microsteps
- Encoder Resolution: 0.0088 degrees
- Default End Effector: Parallel gripper (0-60mm)
- Emergency Stop: Hardware and software implementation
- Weight: 4.8kg
Software Features:
- Native ROS packages available
- Python API with inverse kinematics solver
- Real-time trajectory planning
- Force estimation through motor current
- Built-in collision detection
TinkerArm Pro ($899)
Best for: Beginners with Some Experience
Technical Specifications:
- Joint Speed: 60°/s uniform
- Motor Type: NEMA 14 steppers
- Encoder Resolution: 0.018 degrees
- Default End Effector: Simple gripper (0-40mm)
- Emergency Stop: Software only
- Weight: 2.9kg
Software Features:
- Arduino-based control system
- Basic Python library
- Visual programming interface
- Manual teaching mode
- Simple path recording and playback
MakerBot X7 ($2,199)
Best for: Professional Prototyping
Technical Specifications:
- Joint Speed: 120°/s (base) to 180°/s (wrist)
- Motor Type: Brushless DC with harmonic drives
- Encoder Resolution: 0.0044 degrees
- Default End Effector: Electric parallel gripper (0-85mm)
- Emergency Stop: Dual-channel hardware system
- Weight: 8.2kg
Software Features:
- Full ROS/ROS2 integration
- Comprehensive C++/Python SDK
- Advanced trajectory optimization
- Real-time force control
- Digital twin support
- Machine learning integration capabilities
CraftBot Arm ($1,299)
Best for: Makers and Small Workshops
Technical Specifications:
- Joint Speed: 90°/s uniform
- Motor Type: NEMA 17 steppers with 128 microsteps
- Encoder Resolution: 0.012 degrees
- Default End Effector: Modular quick-change system
- Emergency Stop: Hardware implementation
- Weight: 3.9kg
Software Features:
- Custom Python environment
- Web-based control interface
- Basic path planning
- Gesture control support
- 3D printing integration
EduBot Basic ($599)
Best for: Educational Use
Technical Specifications:
- Joint Speed: 45°/s uniform
- Motor Type: Standard servos
- Encoder Resolution: 0.029 degrees
- Default End Effector: Basic gripper (0-30mm)
- Emergency Stop: Software only
- Weight: 1.8kg
Software Features:
- Blockly visual programming
- Basic Python support
- Classroom management tools
- Simple sequence recording
- Pre-made educational projects
Additional Considerations
Power Consumption
- RoboMaker RT6: 45W typical, 72W peak
- TinkerArm Pro: 24W typical, 35W peak
- MakerBot X7: 65W typical, 96W peak
- CraftBot Arm: 40W typical, 60W peak
- EduBot Basic: 18W typical, 25W peak
Noise Levels
- RoboMaker RT6: 45dB
- TinkerArm Pro: 48dB
- MakerBot X7: 42dB
- CraftBot Arm: 46dB
- EduBot Basic: 50dB
Warranty Coverage
- RoboMaker RT6: 1 year parts/labor
- TinkerArm Pro: 90 days limited
- MakerBot X7: 2 years parts/labor
- CraftBot Arm: 1 year limited
- EduBot Basic: 6 months limited
Recommendations by Use Case
For Learning Robotics
- EduBot Basic – Best budget option
- TinkerArm Pro – Best step-up option
For Maker Projects
- CraftBot Arm – Best overall value
- RoboMaker RT6 – Best feature set
For Professional Use
- MakerBot X7 – Best performance
- RoboMaker RT6 – Best value alternative
For Education Institutions
- EduBot Basic – Best for beginners
- CraftBot Arm – Best for advanced students